Millions of tires are produced every year. However, roughly one tire is disposed of per person each year as well. Since tires are quite durable and are not biodegradable, their disposal can create problems from an ecological perspective. Luckily through the use of pyrolysis tire recycling technology and tire recycling plant many of these tires can be turned into rubber that can be reused.
Ambient mechanical grinding is the cheapest tire recycling technology. It is used to produce crumb rubber. This industry term simply refers to rubber reclaimed from old tires. This particular process can occur at room temperature or in a slightly hotter temperature. There are several steps to this tire reclamation process. First, tires are processed into chips, treads, chips, or sidewalls depending on the machine being used. They can be either pre-treated or used as is also depending on the reclamation pyrolysis machine.
These initial tire remnants are then processed through a shredder. This machine essentially separates the components into rubber, textile. The first part of the process turns the tires into chips if they have not already been reduced to that state prior to arriving on the line. A granulator then breaks down these chips into smaller pieces while at the same time removing any steel or fibers remaining in the chips. High-powered magnets are then used to remove any remaining steel pieces. Shaking screens and wind sifters can be used to remove the smallest pieces of fiber in the remaining mixture. The fine granules left can be made even finer by passing them through another granulator and high-speed mills. The resulting granules are a suitable crumb rubber stock.
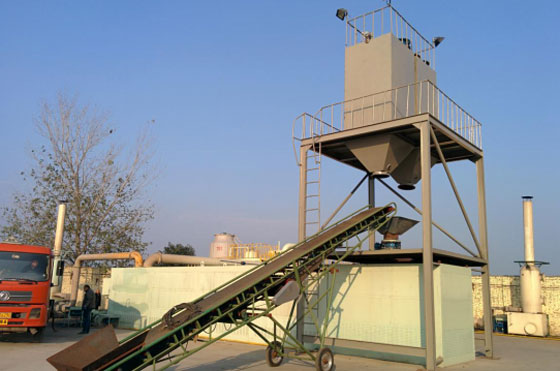
Cryogenic grinding is another waste tires recycling technology commonly used to produce crumb rubber. It is much more expensive to perform; however, the crumb rubber produced by this process is much smoother and comes in smaller granules. The process actually uses less energy to process the tires as well.
In the cryogenic grinding process liquid nitrogen is used to cool initial pre-treated tire chip material to extremely low temperatures in the range of negative 80 degrees Celsius to negative 120 degrees Celsius. This temperature range causes the rubber to become quite brittle. At this point, the rubber can be crushed quite easily, facilitating the process of separating the metal and textile components of the tire. A hammer mill is used as a first state to perform this separation. Once this takes place a series of magnet screens and sifting screens are used to remove the remaining non-rubber materials, similar to the process used in ambient mechanical grinding. Get tyre pyrolysis plant cost here.
Over half of the tires used in the world are not recycled as of the present moment. The increasing use of tire recycling technologies should help to improve the ability to reclaim rubber from tires and prevent tires from filling landfills or being simply used for fuel. This is a more ecologically sustainable solution for tire management with tyre pyrolysis plant.